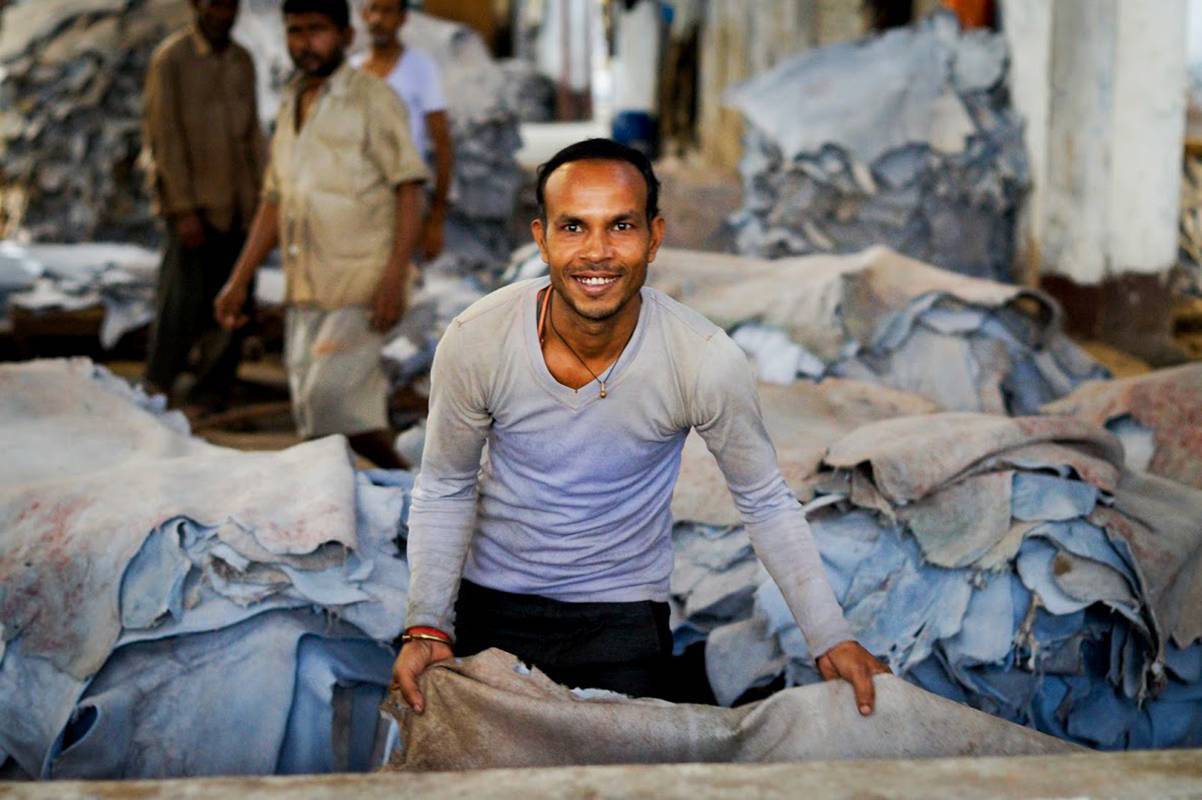
The leather production process generates significant waste, particularly during the liming and fleshing stages, leading to environmental pollution and financial burdens for tanneries. Solidaridad, through the EU funded SWITCH-Asia project named “Effective Waste Management and Sustainable Development of the MSME tanning companies in Kolkata Leather Cluster (Bantala)”, has introduced a sustainable solution for the Kolkata Leather Complex by extracting tallow from fleshing waste. This process involves thermal hydrolysis and acidic purification to separate tallow from the protein-rich residue. The extracted tallow and residue offer commercial opportunities, including soap, paint, and lubricant production. Implementing this initiative not only reduces waste disposal costs but also promotes environmental sustainability and revenue generation for tanners, making the Kolkata leather cluster cleaner and more sustainable. This approach exemplifies the conversion of waste into a valuable resource, supporting a circular economy and enhancing the sustainability of the leather industry.
Introduction:
In the Leather manufacturing process, Liming is one of the most widely practiced and essential method in the tanning industry, typically followed by the fleshing operation. This process has the pivot role of forming high pollutants in the effluent. During fleshing operation, fatty tissues are removed from the flesh side of a hide/skin, resulting in a significant amount of solid waste, accounting for approximately 85% of a beamhouse's and 55% of total tannery waste. This waste contains significant amounts of calcium oxide, sulphates, and small quantities of amines. Historically, it has been disposed of in landfills without treatment, resulting in severe land pollution and groundwater contamination. The environmental impact arises from the putrefaction of this waste in landfills, leading to the release of methane and other greenhouse gases. Additionally, the transportation of this waste by road has caused significant pollution and expenses, which is a serious concern for tannery owners.
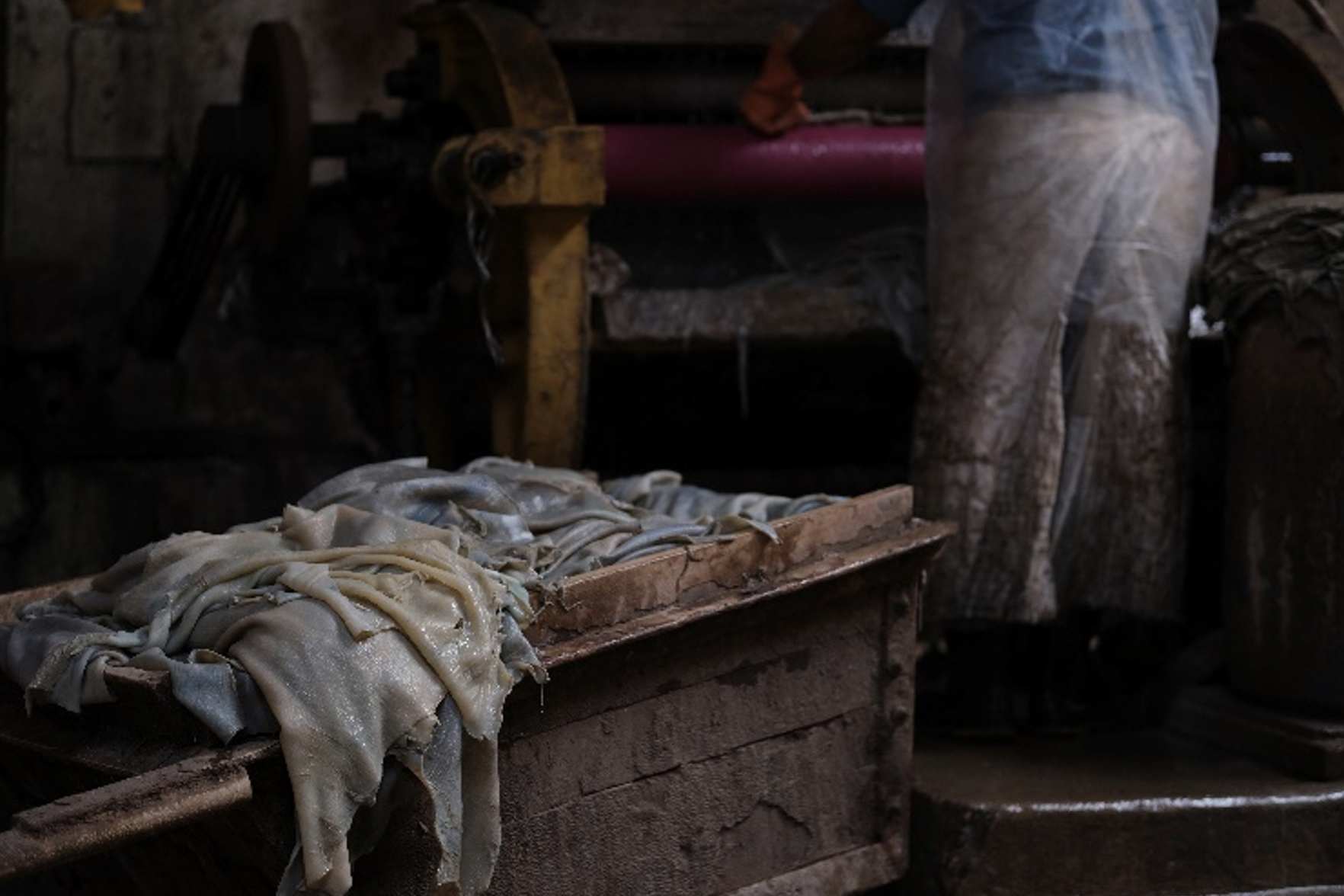
Image 1: - Fleshing Operation
Materials and Methods:
Following a successful demonstration of a 150 kg capacity Tallow Extraction Unit at the CLCTA premises, Solidaridad has established and demonstrated a 4-ton capacity Tallow Extraction Pilot Demonstration Unit at Indian Tanning Industries Pvt. Ltd. This demonstration aims to showcase the business case model and long-term viability for those considering commercial engagement with the technology.
The pilot unit comprises five essential components. The first component is the Fleshing Pit, designed to collect fleshing waste and prepare it for further processing. The second component is a Conveyor Belt connected to the pit, facilitating the transfer of fleshing waste to the cooking vessel without the need for manual labor. The third component is a Mechanical Stirrer, which continuously agitates the mixture inside the vessel to ensure homogeneity before settling. The fourth component is an insulated stainless-steel vessel, where the entire process is conducted for approximately 2.5 hours at a temperature not exceeding 75°C. The fifth and final component is a specialized filter press, used to separate the protein-rich residue and drain excess liquid from the mixture.
Image 2: - Tallow Extractor at ITI
After the cooking process ceases, the triglyceride matter is easily retrieved by opening a designated valve at the top. This material undergoes acidification with industrial-grade inorganic Acid, leading to the separation of tallow from impurities. Through controlled acidification and meticulous filtering, clear and yellow-colored tallow in liquid form is obtained. The settled residue is then directed to a protein pit by opening another valve at the base of the cooking chamber. Subsequently, the protein-based residue is transferred to a filter press for overnight dewatering, resulting in the formation of 95% dried protein-rich chunk.
Results and Impacts:
Following the completion of the process, the extracted tallow, the residual protein-rich cake, and the discharged float from the filter press are sent to laboratories for testing, yielding highly encouraging results.
Tallow Protein Residue
In addition to the test findings, we have also categorized the percentage of tallow/oil that can be extracted based on the substrate type and origin. Through our experience, we have found that the maximum extraction rate from cow substrate ranges from 8% to 9%, from Katta it ranges from 7% to 8%, and from Goat (Indian origin) it is less than 5%.
Cost Benefit Analysis of tallow extraction Unit:
Fleshing waste poses a dual challenge for tanners, serving no purpose in their operations while presenting a logistical headache for removal from tanneries. The costs associated with its unsustainable disposal and transportation are considerable.
For an aspiring entrepreneur, it has been demonstrated that the seemingly worthless daily accumulation of fleshing can be transformed into a lucrative venture with a profitable daily margin. Establishing a production unit of comparable capacity requires factoring in costs such as labor, transportation for collecting fleshings from multiple tanneries, boiler expenses, and the electricity consumption of the tallow extraction unit. Remarkably, the return on investment can be realized within a mere 60 working days.
Benefits:
While there are initial costs associated with adopting this initiative, these costs can be swiftly recouped within two to three months of regular extraction. Both the extracted tallow and protein-rich residue offer significant commercial potential:
1. Abundant in natural fatty acids and possessing moisture-retention properties, these materials can be further processed to create a viable ingredient for soap production.
2. Rich in triglycerides, they can undergo additional treatment to become suitable for the paint industry.
3. Due to their high melting point and anti-friction attributes, they can be further processed into industrial lubricants, offering a more cost-effective alternative to synthetic options and appealing to various industrial lubrication needs.
4. The protein-rich residue from the filter press, a byproduct of the extraction process, can serve as an economical ingredient for animal feed production.
Conclusions:
Leather processing is unique of its kind in transformation from a meat industry byproduct to become a lifestyle material of our daily use. By nature, this is the most ecofriendly and sustainable material. But due to lack of knowledge on managing the solid waste the whole leather industry gets blamed as polluting. This approach of Waste to Wealth conversion not only opens up new possibilities of revenue generation, but also makes the Kolkata leather cluster more sustainable.
As the tallow derived from fleshing waste, byproduct of the leather industry, making it more sustainable resource. Utilizing this tallow reduces waste and promotes a Circular Economy.
Photo credits: EU SWITCH-Asia / Solidaridad: Effective Waste Management and Sustainable Development of the MSME tanning companies in Kolkata Leather Cluster (Bantala)